FARMINGTON CONCRETE
There are endless options in the world of concrete contracting. From structural foundations to artistic implementations, concrete knows no bounds in versatility and functionality. For the customer, the decision of which type of medium to use in their home can be a challenging choice. We strive to make it exceedingly simple to make the right decision for your next hardscape project. Getting a concrete slab installed in Farmington, NM is one of the best decisions a homeowner can make especially if it is being utilized as a driveway, open area, or foundation.
Concrete has stood the test of time and has transcended centuries of testing and innovation. Compared to other hardscape options, concrete reigns superior as the most durable and reliable alternative. At Farmington Concrete, we believe that our customers deserve the best concrete service without breaking the bank.
Regardless of the project size, our team can execute the entire project from excavation and footing, to pouring and finishing. Being a licensed concrete contractor is required in the state of New Mexico to practice legal contracting. Our in-house contractor has over 15 years of concrete contracting experience and holds a current contractor registration. Furthermore, we protect our customers and staff with liability insurance in the event of an accident.
REQUEST A QUOTE
WHY GO WITH US?
Extensive Experience and Reputation
Certifications and credentials are crucial in the world of contracting. However, experience is the true litmus indicator of a concrete specialist’s prowess. There are many excellent concrete contractors in our community that are licensed and experienced like ourselves. What makes our team different is our commitment to delivering the most superior product, every time we are hired for a project. Our schedule is built to allow for maximum quality of deliverables to be served.
Low Pricing
Looking to expand or add-on to your property with a concrete concept? Doing so can be more affordable than you might think. The price of hiring a concrete specialist is often dictated by the size in square feet of the project, as well as the time and resources required to complete the job. For instance, if a customer asks for a concrete pad in their front yard and it is accessible with a concrete truck, it could cost less than if it was not easily accessible. Our rates are competitively paced with local providers to maintain an edge in our small community of Farmington.
Licensed Concrete Contractor
It is illegal in New Mexico to practice contracting without a valid license. Our local concrete contractor is fully licensed and insured and can pull all necessary building permits. It is exceedingly important to vet every contractor before deciding who to hire. Beware of individuals who do not have full licensing and insurance when looking for bids. Often, these people may offer lower prices in exchange for less liability protection. Choosing to hire an unlicensed contractor could result in thousands of dollars in damages or injury.
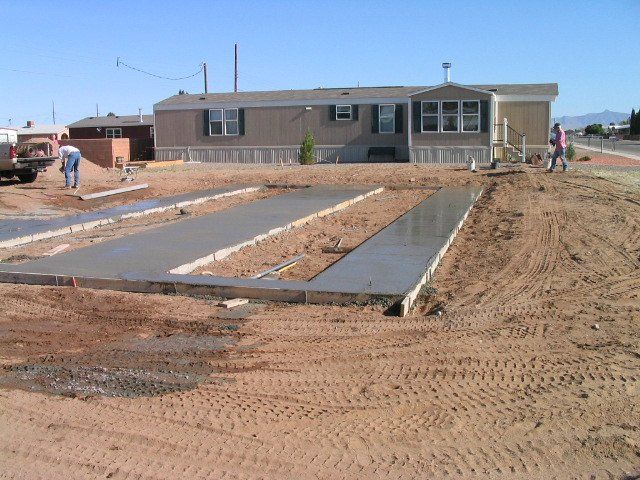
Adequate Insurance and Record of Safety
Having proper licensure and experience should be foundational for all concrete contracting entities in New Mexico. Carrying adequate insurance is required in our state to practice concrete. There are a variety of insurance types to protect the workers, business owner, and customers in the event of a mishap. At Farmington Concrete, we have never had a major incident involving insurance or workers compensation. Our track record of safety harkens back to our extensive experience with concrete and heavy machinery.
CONCRETE MIXING RATIOS
A concrete mix ratio is the proportion of ingredients used to make concrete. The main ingredients in concrete are Portland cement, water, and aggregate (usually sand and gravel). Getting the right mix ratio is important because it determines the strength, durability, and workability of the concrete.
If the ratio is too wet, the concrete will be weak and susceptible to cracking. On the other hand, if the ratio is too dry, the concrete will be difficult to work with and will not set properly. The ideal mix ratio is one that results in a concrete slab that is strong, easy to work with, and cures properly.
The most common concrete mix ratios are 1:2:4 and 1:3:6. These ratios use one part Portland cement, two parts aggregate, and four or six parts water, respectively. These ratios produce a strong, durable concrete that will be suited for most residential construction projects. Other common concrete mix ratios are 1:1:2, 1:2:3, and 1:4:5. These ratios can be used for different purposes, depending on the desired fortitude and manipulability of the concrete. For example, the 1:1:2 ratio is often used for foundations because it produces a very strong concrete. The 1:2:3 ratio is often used for walls because it produces a concrete that is easier to manipulate. And the 1:4:5 ratio is common for floors because it produces a mixture that sets up quickly and allows less time for defects to occur. There are many other concrete mix ratios that can be used, depending on the specific application. However, the 1:2:4 and 1:3:6 ratios are the most commonly used for general purpose concrete applications. The most important thing to remember when making concrete is to get the right mix ratio. The ratio is the proportion of ingredients used to make concrete, and getting it right is crucial to making strong, durable concrete that is easy to work with.
There are a few things to keep in mind when measuring the ingredients for a concrete mix. First, it is important to use the correct measurements. The most common way to measure concrete ingredients is by volume, but weighing the ingredients is more accurate. Second, it is important to use clean, dry ingredients. If the aggregate is damp, it will absorb some of the water from the mix, resulting in a drier mix. And if the Portland cement is clumpy, it will not flow properly and will also result in a drier mix. Third, it is important to add the ingredients in the correct order. The general rule of thumb is to add the dry ingredients first, followed by the wet ingredients. However, some concrete experts recommend adding the wet ingredients first and then the dry ingredients. This helps to prevent the concrete from becoming too dry.
Finally, it is important to mix the concrete thoroughly. The best way to do this is to use a power mixer or a drill with a mixing paddle attachment. Mix the concrete for at least two minutes, or until it is thoroughly combined. Once the concrete is mixed, it is ready to use. Be sure to finish the project within a few hours, as concrete starts to cure quickly. If you need to store the concrete for later use, be sure to cover it with plastic so it doesn't dry out.
Failing to mix concrete properly can result in cracking, breaking, and total foundational failure overtime. If the idea of handling concrete ratios appears overwhelming, you are not alone. For these reasons, we are always available to consult, prepare, and execute a flawless concrete slab. Leaving this type of work to a professional is always a great option if you want things done properly the first time.
OUR SERVICES
Concrete is a reliable building block for foundations, walls, entertaining areas and much more. For millenniums, concrete has been developed to withstand the stresses of foot traffic, buildings, vehicles, and aircraft. With a guaranteed lifespan of 25 years, concrete far surpasses its competitors in the paver and hardwood industry. We are proud to offer a range of services that range from residential to industrial and beyond. The limits and scope of concrete are created only by the imagination of those who wield it.
COMMERCIAL CONCRETE OPTIONS AND CONSIDERATIONS
Pouring concrete is not a one-size-fits-all process. The way it's done depends on the project size and purpose. For residential slabs, the method is usually simpler. A mix of Portland cement, sand, and water is used. However, commercial pads require a stronger mix to bear heavy loads. The size of the project also matters. Residential slabs are smaller and can generally be finished in a day. Meanwhile, commercial pads may take weeks to complete due to their larger size and requirement for additional reinforcement like rebar. Additionally, the thickness of the slab and its intended use will also determine the type of concrete mix used. Understanding these differences is crucial to ensuring that the end result is safe and durable for those who will be walking or driving on it.
IS STAMPED CONCRETE WORTH IT?
When it comes to driveways, walkways and patios, stamped concrete is becoming an increasingly popular choice. It can mimic the look of brick, flagstone, slate or other natural materials at a fraction of the price. But is stamped concrete worth the extra cost?
Stamped concrete is a type of concrete that is textured and patterned to resemble natural stone, brick or other materials that occur naturally. It is a popular choice for driveways, walkways and patios due to its direct indignation of other rock formations. The main advantage of stamped concrete is its price. It is significantly cheaper than natural stone or brick, yet it can still achieve a similar look.
The cost of stamped concrete depends on the size and complexity of the project. For a small patio, it may cost around $8 per square foot. For a driveway, it may cost $15-$20 per square foot. Larger projects can be more expensive depending on what kind of pattern and stain is being used. Despite the higher cost, stamped concrete is a wise investment.
Maintaining stamped concrete is relatively easy when compared to other mediums like asphalt. A sealant should be applied every few years to protect the concrete from staining and fading. In addition, a hose and a broom can be used to clean any dirt or debris from the surface.
There are a variety of stamps that can be used for stamped concrete projects. This includes brick, flagstone, slate and other natural textures. The type of stamp that is used will depend on the look that is desired. For example, a brick stamp can be used to give a patio or driveway a traditional look. A slate stamp can be used to give it a more modern aesthetic.
Stamped concrete is a great way to add value to your home. It is also a wise investment that will save you money in the long run. If you are considering stamped concrete for your next project, be sure to consult with a professional to get an accurate estimate of the cost.
Farmington Concrete is known for delivering high-quality concrete solutions tailored to meet a variety of construction needs. With a reputation built on reliability and craftsmanship, they specialize in providing durable and long-lasting concrete for residential, commercial, and industrial projects. Their commitment to quality begins with sourcing premium materials and using advanced mixing techniques to ensure consistency and strength in every batch.
Whether it’s for driveways, patios, foundations, or decorative concrete, Farmington Concrete emphasizes precision and attention to detail. Their team of skilled professionals ensures that every project is executed to the highest standards, meeting both structural and aesthetic requirements. Additionally, they prioritize customer satisfaction by offering personalized service, timely delivery, and expert advice to help clients achieve their vision.
Farmington Concrete’s dedication to quality and innovation has made them a trusted name in the industry, delivering results that stand the test of time.
Farmington Concrete: Your Community-Focused Partner
At Farmington Concrete, we’re more than just a concrete contractor—we’re dedicated community partners who believe in giving back to the area we serve. Our commitment goes beyond quality construction. We actively support local events, from youth sports teams to school fundraisers, helping strengthen the bonds that make our neighborhoods thrive.
We prioritize partnerships with local businesses, sourcing materials from area suppliers and collaborating with fellow contractors to keep money circulating within our community. Through charitable initiatives and volunteer work on community improvement projects, we show that successful businesses have a responsibility to invest in our neighbors’ success.
Choose Farmington Concrete for your next project and know that you’re supporting a company that genuinely cares about building stronger communities, one relationship at a time.
SIGNS THAT YOU NEED A NEW FOUNDATION
Your home’s foundation is one of the most important parts of the entire structure. It is what keeps your home standing tall and strong, protecting you from the elements and providing a stable base for everything else. That’s why it’s so important to pay attention to the signs that your foundation might be failing. If you notice any of the following, it’s time to call in a professional for an inspection:
1. Cracks in the foundation walls. These can be horizontal, vertical, or stair-stepped, and they are usually wider at the bottom than they are at the top. They might be small and barely visible, or they could be large enough that you can see through them.
2. Gaps where the foundation meets the framing of your house. These are called expansion joints, and they allow for a little bit of movement so that your foundation doesn’t crack. But if the gaps are too big, it means that your foundation is shifting.
3. Doors or windows that stick or won’t close properly. This is usually because the frame has shifted and is no longer level.
4. Cracks in your walls, ceilings, or floors. These can be caused by a number of things, but if they’re located near where the foundation meets the rest of your house, it’s a good indication that there’s a problem with the foundation.
5. Water in your basement or crawlspace. This is a sure sign that there’s something wrong with your foundation, as water should never be able to get in. It could be a cracks or gaps, or it could be that the ground around your foundation is too high and needs to be graded away from the house.
If you notice any of these signs, don’t delay in getting it checked out. The sooner you address the problem, the less damage there will be and the easier it will be to fix. A professional concrete contractor can assess the situation and recommend the best course of action.